
Iron Ore Processing an overview ScienceDirect Topics
In India, where iron ore processing is one of the major industries, the generation of tailings is estimated to be 1025 % of the total iron ore mined, amounting to 18 million tons per SINTERING AND PELLETISATION OF INDIAN IRON ORES,Bangalore IRONORESUPPLYDEMANDSCENARIOININDIA (20002040) NEEDFORBENEFICIATION Highgradeironorelessthan10%ofthetotalreserves.

Auctioning of Indian mining leases and the iron ore
1029· The Odisha government has invited bids for seven iron ore blocks on October 4, after a delay of more than a year. Given that Existing and New Processes for Beneficiation of Indian ,28· The iron ore industries of India are expected to bring new technologies to cater to the need of the tremendous increase in demand for quality ores for steel making.

India Mining & Mineral Processing Equipment
1013· Overview. India possesses significant mineral resources, ranking among the top ten global producers of mica, barites, coal and lignite, iron ore, chromite, bauxite, Iron processing Definition, History, Steps, Uses, & Facts,iron processing, use of a smelting process to turn the ore into a form from which products can be fashioned. Included in this article also is a discussion of the mining of iron and of

Mineral Processing Thriveni Earth Movers Pvt Ltd
In Iron ore and Coal, mineral processing plays a vital role. Our expertise lies in design, engineering, procurement, installation and commissioning a mineral processing plant. Five largest iron ore mines in India in Mining ,97· Here are the five largest iron ore mines by production in India, according to GlobalData’s mining database. 1. Bailadila Iron Ore Mines (Kirandul Complex) The

Iron Ore Processing Plant Iron Ore Processing Plant
Creating steel from lowgrade iron ore requires a long process of mining, crushing, separating, concentrating, mixing, pelletizing, and shipping. Call Now: +919909006104Existing and New Processes for Beneficiation of Indian Iron ,28· This is mainly due to the reason that most hematite iron ores of India are very soft, generating around 35–40% of fines and slime during the process of mining, beneficiation and preparation of sized ore. The tailings and slimes generated from the hematite ores are 10–30% of the run of the mines and are discarded as waste [ 4 ].

JSW Vijayanagar Works Overview
Employs a largescale, lowgrade iron ore beneficiation process; Uses pelletisation based on dry and wet process; Is the only plant with a combination of both nonrecovery and recovery type of coke ovens; Is the only plant in India with paircross technology and twinstand reversible coldrolling millIron & Steel Industry in India: Production, Market Size, Growth,In AprilNovember , the production of crude steel and finished steel stood at 81.96 MT and 78.09 MT respectively. The growth in the Indian steel sector has been driven by the domestic availability of raw materials such as iron ore and costeffective labour. Consequently, the steel sector has been a major contributor to India's manufacturing

Investigation on Iron Ore Grinding based on Particle Size
528· The feed samples of X, Y, and Z iron ores were ground in the BBM (ball mill refers to a BBM of size 300 mm × 300 mm with smooth liners) to identify the PSD, BWI, and RT of each ore. Grinding experiments were conducted according to Bond’s standard test procedure .For each iron ore sample, the RT taken to produce 250% circulating Iron and steel industry in India Wikipedia,Sahi (1979: 366) concluded that by the early 13th century BCE, iron smelting was practiced on a larger scale in India, suggesting that the date the technology's early period may well be placed as early as the 16th century BCE. [7] Some of the early iron objects found in India are dated to 1400 BCE by employing radiocarbon dating. [9]

The six main steps of iron ore processing Multotec
3. Feeding the crusher (Reclaim) The surge pile allows a constant supply of material to be fed into the mill, which ensures consistent results and stability in the ore recovery process. 4. Grinding. The primary grinding mill grinds the material before it Mineral Processing Thriveni Earth Movers Pvt Ltd,In Iron ore and Coal, mineral processing plays a vital role. Our expertise lies in design, engineering, procurement, installation and commissioning a mineral processing plant. Our own EPCC team has designed and commissioned one of the biggest processing plants in India i.e. 1500 tph Central Processing Unit in Balda Block Iron ore mines, which

A short review on environmental impacts and application of iron ore
11· The IOT are stored on the open fields such as dumping dams or embankments, and the quality and quantity of the IOT generated depends on the mining site and grade of the ore. In India the ore extraction varies between 35% and 65% of the total mined material, and rest of it becomes waste due to lack of advanced beneficiation Iron Ore Processing Plant Iron Ore Processing ,Screening: The first one is screening the iron ore to separate fine particles below the crusher’s CSS before the crushing stage.; Crushing and stockpiling: This step involves breaking up the iron ore to obtain an F80

Grindability Studies of Mineral Materials of Different
Comminution is a popular process in mineral, cement, pharmaceutical, refractory, fertilizer and chemical industries. India. Banded Iron Formations are chemically precipitated enigmatic rocks constituting alternate ironrich and Density and Moh’s hardness of studied iron ore samples are given Table 1 & Figure 1 shows hard and fineSintering: A Step Between Mining Iron Ore and ,611· According to the U.S. Environmental Protection Agency, the sintering process converts finesized raw materials, including iron ore, coke breeze, limestone, mill scale, and flue dust, into an agglomerated

Recycling of steel plant mill scale via iron ore pelletisation process
20131129· Abstract. Mill scale is an iron oxide waste generated during steelmaking, casting and rolling. Total generation of mill scale at JSWSL is around 150 t/day and contains 60–70%FeO and 30–35%Fe 2 O 3.To recover the iron, the mill scale must be smelted in a blast furnace or other reduction furnace; however, it is usually too fine to use without Iron ore Wikipedia,This determines the energy inputs required to run a milling operation. Mining of banded iron formations involves coarse crushing The total recoverable reserves of iron ore in India are about 9,602 million tonnes

Advances in Low Grade Iron Ore Beneficiation MECON
The Kudremukh plant in Karnataka was the first big iron ore beneficiation plant in India. It mainly processes complex haematite and magnetite ore. It got pelletisation facility for pellet making from the concentrate of beneficiation plant. Pellets are not for domestic consumption rather exported for revenue generation.JSW Vijayanagar Works Overview,Employs a largescale, lowgrade iron ore beneficiation process; Uses pelletisation based on dry and wet process; Is the only plant with a combination of both nonrecovery and recovery type of coke ovens; Is the only plant in India with paircross technology and twinstand reversible coldrolling mill

Iron & Steel Industry in India: Production, Market Size, Growth
In AprilNovember , the production of crude steel and finished steel stood at 81.96 MT and 78.09 MT respectively. The growth in the Indian steel sector has been driven by the domestic availability of raw materials such as iron ore and costeffective labour. Consequently, the steel sector has been a major contributor to India's manufacturingIron and steel industry in India Wikipedia,Sahi (1979: 366) concluded that by the early 13th century BCE, iron smelting was practiced on a larger scale in India, suggesting that the date the technology's early period may well be placed as early as the 16th century BCE. [7] Some of the early iron objects found in India are dated to 1400 BCE by employing radiocarbon dating. [9]

Mineral Processing Thriveni Earth Movers Pvt Ltd
In Iron ore and Coal, mineral processing plays a vital role. Our expertise lies in design, engineering, procurement, installation and commissioning a mineral processing plant. Our own EPCC team has designed and commissioned one of the biggest processing plants in India i.e. 1500 tph Central Processing Unit in Balda Block Iron ore mines, whichThe six main steps of iron ore processing Multotec,Six steps to process iron ore 1. Screening We recommend that you begin by screening the iron ore to separate fine particles below the crusher’s CSS before the crushing stage. A static screen is used to divert the fine particles for crushing. This step prevents overloading the crusher and increases its efficiency.
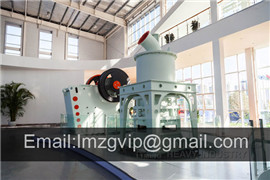
A short review on environmental impacts and application of iron ore
11· The IOT are stored on the open fields such as dumping dams or embankments, and the quality and quantity of the IOT generated depends on the mining site and grade of the ore. In India the ore extraction varies between 35% and 65% of the total mined material, and rest of it becomes waste due to lack of advanced beneficiation Iron Ore Processing Plant Iron Ore Processing ,Screening: The first one is screening the iron ore to separate fine particles below the crusher’s CSS before the crushing stage.; Crushing and stockpiling: This step involves breaking up the iron ore to obtain an F80

Vertical mill simulation applied to iron ores ScienceDirect
41· Abstract. The application of vertical mills in regrind circuits is consolidated. This type of mill is now attracting interest in primary grinding applications, due to its higher efficiency when compared to ball mills, which are usually used at this stage. In this study, a coarse sample of iron ore was tested in a pilot scale grinding circuitAdvances in Low Grade Iron Ore Beneficiation MECON,The Kudremukh plant in Karnataka was the first big iron ore beneficiation plant in India. It mainly processes complex haematite and magnetite ore. It got pelletisation facility for pellet making from the concentrate of beneficiation plant. Pellets are not for domestic consumption rather exported for revenue generation.

Sintering: A Step Between Mining Iron Ore and
611· According to the U.S. Environmental Protection Agency, the sintering process converts finesized raw materials, including iron ore, coke breeze, limestone, mill scale, and flue dust, into an agglomerated Investigation on Iron Ore Grinding based on Particle Size,528· The feed samples of X, Y, and Z iron ores were ground in the BBM (ball mill refers to a BBM of size 300 mm × 300 mm with smooth liners) to identify the PSD, BWI, and RT of each ore. Grinding experiments were conducted according to Bond’s standard test procedure .For each iron ore sample, the RT taken to produce 250% circulating

Iron ore Wikipedia
This determines the energy inputs required to run a milling operation. Mining of banded iron formations involves coarse crushing The total recoverable reserves of iron ore in India are about 9,602 million tonnes Recycling of steel plant mill scale via iron ore pelletisation process,20131129· Abstract. Mill scale is an iron oxide waste generated during steelmaking, casting and rolling. Total generation of mill scale at JSWSL is around 150 t/day and contains 60–70%FeO and 30–35%Fe 2 O 3.To recover the iron, the mill scale must be smelted in a blast furnace or other reduction furnace; however, it is usually too fine to use without

Glossary of Terms/ Definitions Commonly Used in Iron & Steel
HOT METAL (LIQUID IRON): It is the hot, liquid, metallic iron product obtained upon reduction of iron ore (normally in Blast Furnace or in Corex Furnace). It contains about 9394% Iron (Fe) and other elements/impurities like Carbon (4%), Silicon (~1%), Manganese (+1%) Sulphur, Phosphorus etc. Hot metal is the primary input for production of,
- ماكينة صناعة الديول البوراك
- مسحوق جاف طاحونة للصيدلة
- دراسة الجدوي خلاطة اسفلت
- مصانع غسل الذهب للبيع مصر
- تبحث عن شريك تعدين الرخام
- المشترين كسارة الحجر في تنزانيا
- الحجر المستخدمة سحق آلة في زامبيا
- مطحنة عمودية للبيع في جورجيا
- benefits of coal extraction
- الكربون المنشط بالجملة الموردين
- التعدين المكثف جولد جولد التعدين
- رمح كسارة الحجر الجيري
- سحق الصور وفرز النباتات في صناعة التعدين
- خطط معدات التنقيب عن الذهب المنزل
- معدات الصين مطحنة الكرة
- آلة كسارة متنقلة في نيجيريا
- كسارة الحجر والمحجر النباتي في سوريجاو، الفلبين
- سعر الكسارة المخروطية 4 1
- منطقه آسیاب کراچی جاده سند پاکستان
- سعر كسارة الحجارة الصغيرة في نافي مصر